Over the past two decades, China’s mould manufacturing technology has made a qualitative leap. The mould industry has risen rapidly from small to large. With the development of China’s automotive industry, independent brands have marched towards the middle and high-end, and new energy vehicles have sprung up. China has stepped into the ranks of the world’s powerful mould industry.
The world’s powerful mould countries are China, Germany, the United States, Italy, Australia, Singapore and Japan. Today we will analyze the advantages of each country’s mould:
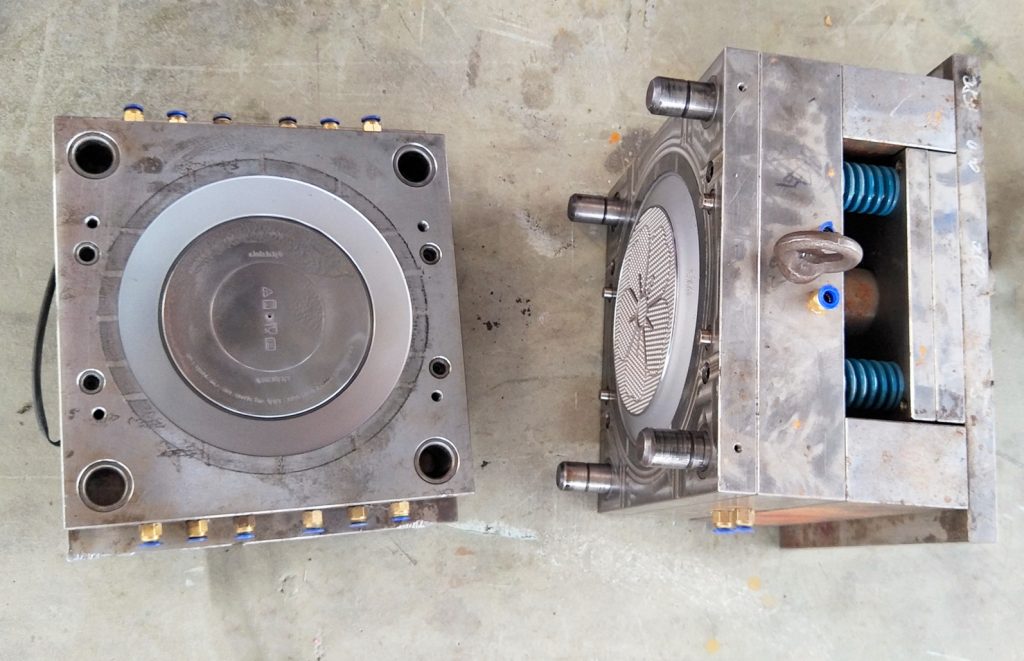
German mould manufacturing technology is exquisite
Germany has always been famous for its exquisite processing skills and the production of precision machinery and tools. Its die industry fully reflects this feature. In order to meet the needs of the rapid development of new products, not only large companies in Germany have established new development centers. But also many small and medium-sized enterprises have done so, taking the initiative to do research and development work for customers. Germany has always been very active in research and has become an important basis for its invincibility in the international market.
In the fierce competition, the German mould industry has maintained a strong position in the international market for many years. And the export rate has been stable at around 33%. According to the statistics of the German Federation of Machinery Manufacturers (VDMA), there are about 5000 mould enterprises in Germany. In 2003, the output value of German mould reached 4.8 billion euros. Among them (VDMA) member mould enterprises have 90. And the output value of these 90 backbone mould enterprises accounts for 90% of the output value of German mould.
Italian Mould Quality and Efficiency
The production technology level of Italian mould enterprises is first-class in the world. According to Luo Baihui, the executive secretary of the International Association of Suppliers of Mold and Hardware and Plastics Industry. The application of high and new technology in mould design and manufacturing has become a strong guarantee for rapid manufacturing of high-quality mould in Italy. In Italian mould enterprises, CAD/CAE/CAM, high-speed cutting technology, rapid prototyping technology and rapid tooling technology have become widely used technologies.
The wide application of CAD/CAE/CAM shows the superiority of using information technology to drive and promote the die and mould industry.
In the application of CAD, it has gone beyond the initial stage of throwing away the drawing board and two-dimensional drawing. At present, the 3D design has reached 70%-89%. PRO/E, UG, CIMATRON and other software are widely used. 2D design & 3D model software provides a guarantee for the integration of NC programming and CAD/CAM. Using 3D design, assembly interference can be checked during design to ensure the rationality of design and process. The universal application of NC machine tools ensures the processing accuracy and quality of die parts.
Die and mould enterprises with 30 to 50 people generally have more than 10 CNC machine tools. Parts processed by NC machine tools can be assembled directly, which greatly reduces the number of fitters. CAE technology has gradually matured in Italy. In the design of injection mould, CAE analysis software is used to simulate the process of plastic stamping die. And analyze the cooling process and predict the possible defects in the process of forming. CAE software is used to simulate the metal deformation process, analyze the distribution of stress and strain, and predict the defects such as cracking, wrinkling and springback. CAE technology plays a more and more important role in die design. With the application of CAE technology by Italian COMAU Company, the time of die test has been reduced by more than 50%.
In order to shorten the die-making cycle and improve the market competitiveness, high-speed cutting technology is widely used.
High-speed cutting is a processing technology characterized by high cutting speed, high feed speed and high processing quality. Its processing efficiency is several times, even more than ten times, higher than that of traditional cutting technology. At present, the Italian die and mould enterprises widely use NC high-speed milling in production. There are many three-axis linkage, some are five-axis linkage, the rotational speed is generally 15,000-30,000 r/min.
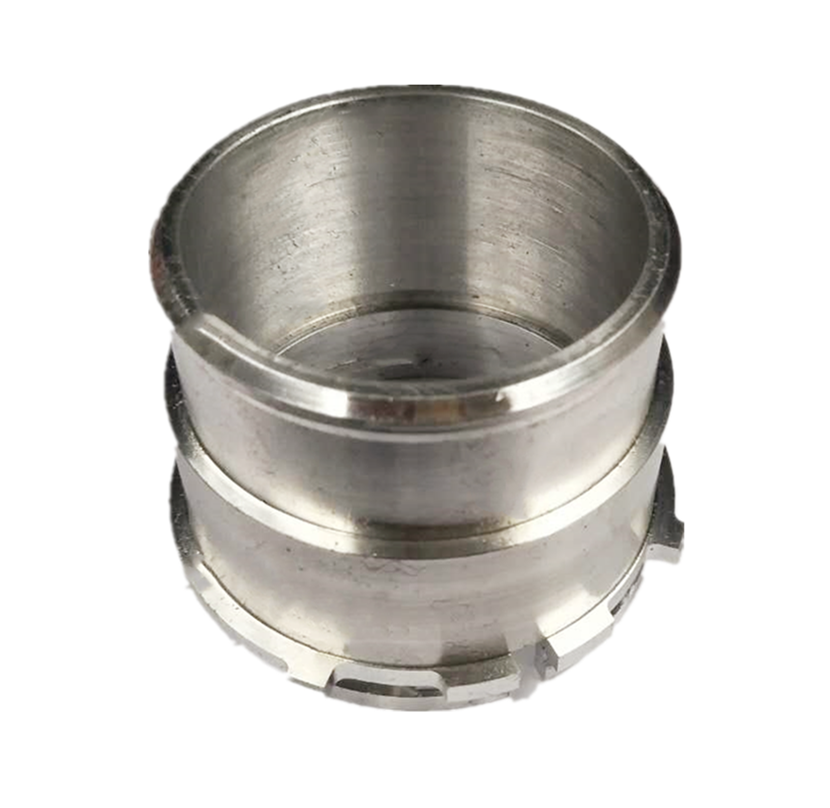
Using high-speed milling technology can greatly shorten the time of moulding.
After high-speed CNC milling and finishing, the die surface can be used only with slight polishing, which saves a lot of time for grinding and polishing. Italian mould enterprises attach great importance to technological progress and equipment updating. The depreciation period of equipment is generally 4 to 5 years. Increasing NC high-speed milling machine is one of the key points of equipment investment in die and mould enterprises.
Rapid prototyping technology and rapid tooling technology have been widely used.
Due to the increasingly fierce market competition and the acceleration of product updating, rapid prototyping and rapid tooling technology emerged as the times require, and quickly gained universal application. Rapid prototyping technology and rapid prototyping technology occupy a prominent position in European and American mould exhibitions such as Italy. There are various types of rapid prototyping equipment such as SLA, SLS, FDM and LOM, as well as institutions and companies specializing in prototyping services.
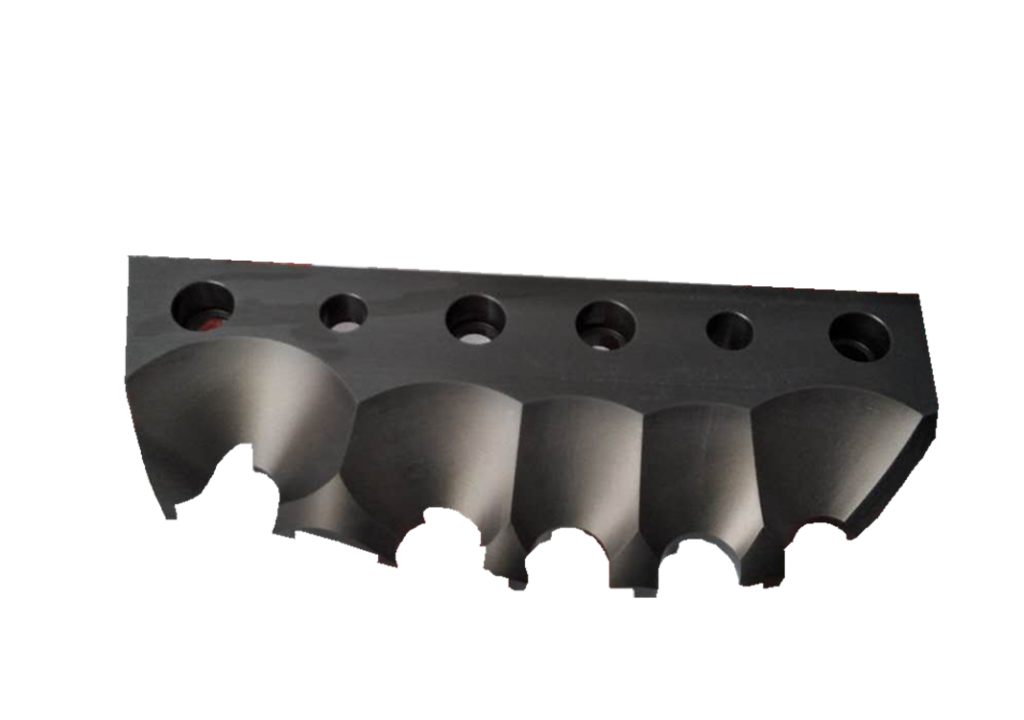
Many Italian die and mould enterprises apply rapid prototyping technology and rapid tooling technology to die manufacturing. That is, using rapid prototyping technology to manufacture prototypes of product parts, and then rapidly manufacturing dies based on prototypes. Many plastic mould manufacturers use rapid prototyping to make silicone rubber mould. Which is suitable for a small number of plastic parts, and is very suitable for trial production of products.
Italian plastic and rubber processing machinery and mould manufacturing industry is one of the 10 special machinery manufacturing industries. And has more than 500 European patents, with high degree of specialization, leading technology and diverse products. Providing customers with a variety of value-added Service. According to Luo Baihui, the annual sales per capita of Italian mould enterprises are over 100,000 US dollars.
With advanced technology and management, Italian mould enterprises have produced large, precise and complex moulds. Which play an extremely important role in promoting the development of automobile, electronics, communications, household appliances and other industries. And also bring good economic benefits to the mould enterprises.
Moulds Making in the United States are facing change
There are about 7000 die and mould enterprises in the United States, more than 90% of which are small enterprises with less than 50 people. Because of the high development of industrialization, American mould industry has already become a mature high-tech industry.
Standardized production and supply of die steel has been realized in the United States. CAD/CAE/CAM technology is widely used in die design and manufacture. Advanced equipment is used for processing technology, inspection and testing. The development of large, complex, precise, long life and high performance die has reached the leading level. Since the 1990s, the US economy has been facing great adjustment and change in the post-industrialization era, as well as strong international competition – from cost pressure, time pressure and competition pressure.
Japan Masters Core Technology of mould manufacturing
Japan’s die and mould industry has always maintained the status of the world’s largest die and mould power. At its peak in 1998, its total domestic output of die and mould reached 1895.4 billion yen. However, in the 10 years since then, although the annual output value has risen or fallen. The overall situation has stagnated and has not recovered or surpassed the level in 1998, and the number of mould manufacturing enterprises has also shown a decreasing trend year by year.
At present, it is necessary to be vigilant that international hedge funds and capitalists, by creating public opinion, exaggerating losses and taking advantage of the opportunity to withdraw funds, will have a serious impact on the development of the global economy. If Japanese capital is withdrawn, the global industrial associations will be greatly impacted.
Some of them have begun to close down, and the number of enterprises is decreasing month by month. Faced with this situation, Japanese die and mould industry people are very worried about the brain drain, especially about the flow of older and experienced talents abroad. The brain drain will bring disadvantage to the future development of Japanese industry. How to actively deal with the current difficulties has become a major issue in Japanese die and mould industry. Japan’s die and mould industry and even the relevant government departments have given much consideration to the future development direction of its die and mould industry.
From the point of view of the people, Japan has put forward six main directions of development:
- To adopt as many high and new technologies as possible to improve the level of digitalization and informatization;
- Developing new fields of mould application, such as various new energy sources, new materials, medical treatment, aerospace and other fields;
- Extending the mould industry chain;
- Developing diversified management;
- Updating knowledge;
- Do a good job in the combination of development, production, education and research.
At the government level, the Ministry of Economy and Industry of Japan has organized a “Material Technology Strategy Seminar Committee” and issued a “Material Technology Strategy” which belongs to the nature of guidelines. The goal of implementing this technology strategy is very clear, that is, to grasp the lifeline of world manufacturing industry by mastering the important technology of material and shape materials.
New Requirements for Application of Mould Manufacturing Equipment in China
On April 10, 2018, Qin Ke, Secretary-General of China Mold Industry Association, made a keynote report on “Coexistence and Co-development of China Mold Industry and Modern Manufacturing Industry” at CCMT 2018. Which covered the market situation, equipment situation, future development direction of the mould industry and its demand for equipment.
Mould innovation and technological progress are accelerating. New technologies, new materials and new forms drive the new structure and new products of mould. The driving characteristics of technological innovation are obvious. Mould industry innovation has changed from tracking to tracking and running in a new stage.
Fineness, automation, informationization, integration, networking and intellectualization will accelerate the improvement of quality, efficiency and optimization of the industry. Die products will continue to develop in the direction of large-scale, precision, high-performance and integration.
Mould manufacturing puts forward new requirements for itself and equipment application. Through equipment utilization rate evaluation, manual interference evaluation, collaborative evaluation, product quality evaluation, etc. Die processing is developing towards high precision and high efficiency. In die manufacturing, we pursue modularization, standardized technical specifications and process management of non-standard products, and strive to achieve the integration of precision control, intelligent monitoring, stable production and quality control.
Die and mould enterprises have put forward the application level indicative requirements for die and mould manufacturing equipment:
- improve equipment utilization rate, man-machine ratio optimization step by step;
- benchmark, knowledge base management, parts, modular manufacturing;
- automation of processing units;
- a large number of dedicated equipment into die and mould manufacturing, such as multi-axis multi-path intelligent dedicated equipment;
- Implementation of manufacturing process control and result management.
Singapore concentrates on the development of IT moulds
Singapore is a small country with a population of only 3 million. In the 1980s and 1990s, the government attached great importance to and supported the development of precision moulds. Many policies were introduced, which made the mould industry grow rapidly and promoted the rapid development of Singapore’s economy.
Singapore has more than 1,000 enterprises of various types of moulds and precision processing. The annual output value of moulds exceeds 4.5 billion RMB, which has a considerable influence and role in the Asian moulds industry. There are more than 10 mould enterprises listed on the market. More than 65% of the moulds produced by enterprises in Singapore are matched by IT electronics related industries.
The moulds produced are not large-scale, but high-precision and high-level moulds. Singaporean die and mould enterprises mainly focus on semiconductor frame/package die, metal stamping die, plastic die, silicone rubber die and other fields.
Auto stamping die available in Australia
Australia has developed rapidly in recent years and will continue to grow in the coming years. However, die manufacturing industry, especially stamping die manufacturing capacity, can not meet the needs of economic development. Therefore, it is urgent to import stamping die manufacturing technology and capabilities from abroad.
Most of the software used in the design and manufacture of automotive die in Australia are ug, pro-e, CATIA and euclid. Which are basically the same as those used by Chinese die enterprises and can be shared. There are similarities between the CAE analysis software and the simulation shaping analysis software. This provides a good condition for us to carry out Sino-foreign cooperation.
Australian Mold Association, Adelaide Mould Office and Melbourne Mold Association all place great hopes on China’s mould Market and manufacturing enterprises. This will create favorable conditions for China to export mould to Australia.
MORE INFORMATION ABOUT KYLT CNC MACHINING SERVICE– CNC MILLING, CNC TURNING, RAPID PROTOTYPING, PLEASE CONTACT US: WECHAT: (86) 15195010186 EMAIL: STONECHENPENG@ALIYUN.COM
KYLT CNC Machining Services:
Home>CNC Machining Services>CNC Milling Services
Home>CNC Machining Services>CNC Turning Services
Home>CNC Machining Services>Rapid Prototyping Services
Home>CNC Machining Services>Injection Molding Services
KYLT CNC Precision Machined Parts:
Home>Precision CNC Machined Parts
Home>Precision CNC Machined Parts>CNC Precise Turned Parts
Home>Precision CNC Machined Parts>CNC Precise Milled Parts
Home>Precision CNC Machined Parts>Aluminum Machining
Home>Precision CNC Machined Parts>Magnesium Machining
Home>Precision CNC Machined Parts>Copper & Brass Machining
Home>Precision CNC Machined Parts>Steel Machining
Home>Precision CNC Machined Parts>Stainless Steel Machining
Home>Precision CNC Machined Parts>Plastic Machining
More information about Machining Technology: