KYLT CNC Machining Services and Rapid Manufacturing Company From China
KYLT CNC Machining Services and Rapid Manufacturing Company from China provide exceptional services in the field of CNC machining and rapid manufacturing. With over 15 years of experience, KYLT specializes in working with magnesium alloy CNC machining, as well as Mold, Jig, Checking tools, Fixtures design and production. Our skilled team is capable of working with various materials such as Aluminum, Stainless steel, Steel, Magnesium, Copper, and Plastic, delivering CNC turning and milling parts that boast high precision, excellent surface quality, and thin walls.
Min. Volume and Fast Prototype CNC Machining Service
At KYLT, we offer CNC machining services for projects of any volume, from prototyping to mass production runs. Our experienced engineers can analyze and program your parts using computer-aided design, ensuring seamless integration with our CNC manufacturing process. Our efficiency allows us to deliver your project within 1 hour of receiving the instructions. To get started with our services, please reach out to us via email at cnkylt@aliyun.com.
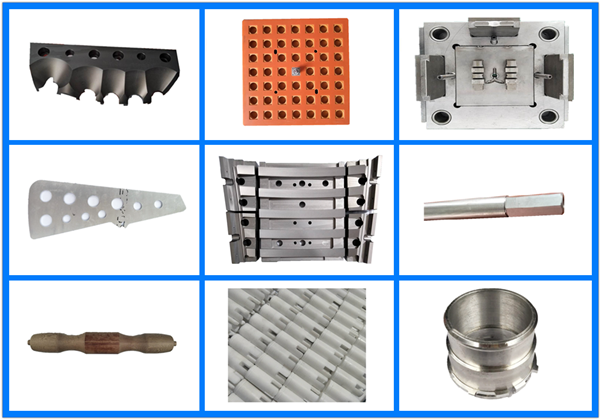
From prototyping to mass production runs. Our engineers analyzed & programmed your part from computer to CNC manufacturing within 1 hour.
SERVICE Email: cnkylt@aliyun.com
KYLT CNC Machining Services Advantages:
KYLT CNC Machining Services has numerous advantages that set us apart from our competitors:
-
Extensive Experience: With over 15 years of experience, we have successfully worked on Aluminum and Magnesium CNC machining projects for defense, commercial, and export markets, including the United States, Canada, Germany, Japan, Spain, the Netherlands, and more. We specialize in producing magnesium alloy CNC machining products with thin walls, particularly for the army industry.
-
Skilled Engineers: Our team consists of experienced engineers with exceptional skills in programming, mold and fixture design, and the production of high-quality workpieces. We utilize industry-standard software such as Proe, UG, Solidworks, Mastercam, and CAD to ensure the utmost precision and accuracy.
-
OEM and ODM Services: We provide OEM (Original Equipment Manufacturer) and ODM (Original Design Manufacturer) services, allowing us to customize our offerings to meet the unique requirements of our customers.
-
Quick Turnaround Time: We understand the importance of meeting deadlines. Therefore, we offer tight schedules and quick prototype manufacturing to guarantee on-time delivery. Our team works tirelessly, 24 hours a day, to ensure prompt service.
-
Flexible Order Quantity: Whether you require a single piece or up to 2000 pieces, we can accommodate your needs. Our MOQ (Minimum Order Quantity) is flexible, ensuring that we can meet your specific demands.
-
Safe Packaging and Shipping: We prioritize the safety of your workpieces during transit. Our team employs the best packaging practices to prevent any damage. Additionally, we offer various shipping methods, including vessel, air, and express options (TNT, FedEx, DHL, etc.), enabling you to choose the most suitable method based on your requirements.
To receive a quotation for your CNC machining project, please Email us: cnkylt@aliyun.com OR click GET A QUOTE
CNC Machining Services Processes:
At KYLT, we offer a comprehensive range of CNC machining services:
1. CNC Machining Capabilities:
Our 3 and 4-axis machine centers provide precision CNC machining services for diverse industries. We work with a wide range of materials, including both ferrous and non-ferrous metals, as well as plastics. From prototyping to full-scale production. No Min. Quantity limit, from 1pcs prototype sample to 20,000pcs full production is acceptable.
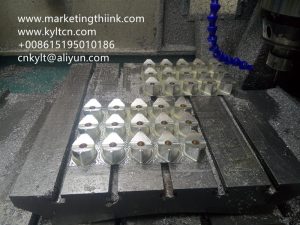
2. CNC Milling service:
Our CNC milling service offers high-precision machining for complex parts and components. With advanced milling machines and cutting-edge software, we can efficiently produce intricate designs with tight tolerances. Whether you require simple or complex geometries, our skilled technicians ensure excellent surface finishes and dimensional accuracy.
Steel parts milled by CNC machine center
More about KYLT CNC milling capabilities
3. CNC TURNING SERVICE:
CNC turning produces parts with cylindrical features by removing material from metal or plastic rods using cutters, and center drills.
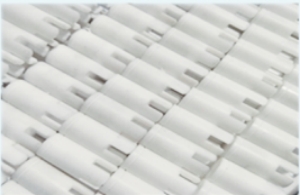
More about KYLT CNC turning capabilities
4. 3-axis & 4-axis CNC machining:
Different designed parts deal with different programs, and 3-axis & 4-axis CNC routers & Milling machines are used to meet different demands.
CNC Machining Services Offered:
- 3 axis Machining
- 4 axis Machining
- Aluminum Machining
- Magnesium Machining
- Copper/ Brass Machining
- Carbon Steel Machining
- Stainless Steel Machining
- NC Lathe
- CNC Turning
- Small Plate Work
- Precision Machining
- Custom CNC Work
- Small Batch Production
- Prototype CNC Work
Click GET A QUOTE to get a free quotation for your CNC machining work-piece price.
Or Email us: cnkylt@aliyun.com
CNC Machining Working Materials:
1. CNC MACHINING METALS:
- Aluminum: High machinability and ductility, good strength-to-weight ratio.
- Brass: Low friction, excellent electrical conductivity, golden appearance.
- Steel:
- Mild steel: High machinability and weld-ability, high stiffness.
- Alloy steel: High strength and toughness, fatigue resistant.
- Tool steel: High hardness and stiffness, abrasion resistant.
- Stainless Steel: High tensile strength, corrosion and temperature resistance.
Click GET A QUOTE to get a FREE quotation for your Metal CNC machining part price.
Or Email us: cnkylt@aliyun.com
2. CNC MACHINING PLASTIC:
- Plastic
- ABS: Common thermoplastic, impact resistant, easy to machine.
- Poly-carbonate: High toughness, excellent impact strength, transparency.
- Nylon: Excellent mechanical properties, thermal, chemical and abrasion resistant.
- POM (Delrin): High stiffness, high accuracy, low friction, easy to machine.
- PTFE (Teflon): Low friction, chemical and thermal resistant.
- Polyethylene: Excellent strength-to-weight ratio, impact and weather resistant.
- PEEK: High-performance thermoplastic, very high strength, thermal and chemical resistant.
- PVC: Excellent corrosion resistance, insulation and certain mechanical strength.
- Custom Materials
Click GET A QUOTE to get a free quotation for your Plastic CNC machining part price.
Or Email us: cnkylt@aliyun.com
CNC Machined Parts Finishes Available:
As Machined – This is a quick affordable choice often used for nonshow applications such as mounting brackets. However, cutter marks from the CNC Machining process will be present.
Sand Paper #320 – A light sandpaper will remove the cutter marks left over from the CNC machining process, but will leave behind a uniform grit (scratch pattern) from the sandpaper.
Sand Paper #400 – A smoother alternative to 320 Paper
Shot Blasting – This will remove light cutter marks and light sandpaper scratches, leaving behind a smooth uniform sheen.
Shacking polish – Stone, Stainless Steel balls give parts a smooth surface for painting.
Anodizing – Corrosion Prevention and aesthetics.
Custom Coatings & Finishes – Painting and Powder coating are allowed.
More information about KYLT CNC MACHINED PARTS– CNC MILLING, CNC TURNING, RAPID PROTOTYPING, Please Contact US: Wechat: (86) 15195010186 Email: cnkylt@aliyun.com
More information about KYLT PLASTIC MOULDING PARTS, die casting parts (ALUMINUM DIE CASTING, ZINC/ZAMAK DIE CASTING), Please Contact US: Wechat: (86) 15195010186 Email: cnkylt@aliyun.com
FAQ
-
What is CNC machining?
CNC (Computer Numerical Control) machining is a process that uses computerized machines to create precise parts and products from raw materials such as metal, plastic, or wood. The CNC machine reads instructions from a computer program and translates them into movements of the cutting tool, allowing for highly accurate and repeatable manufacturing processes. This technology is widely used in industries such as aerospace, automotive, medical devices, and many others where precision manufacturing is essential.
-
What is meant by CNC machining?
CNC machining is a manufacturing process that involves using computer-controlled machines to create precise and complex parts from raw materials. The term “CNC” stands for Computer Numerical Control, which refers to the use of software to control the movement and operation of machines. CNC machines use rotating cutting tools to remove material from the workpiece, guided by instructions from a computer program. This allows for highly accurate and repeatable manufacturing processes, making it a preferred method for producing high-quality parts in industries such as aerospace, automotive, medical devices, and many others.
-
What are CNC machines used for?
CNC machines are used to create precise and complex parts from raw materials such as metal, plastic, wood, and composites. They are widely used in various industries, including aerospace, automotive, medical devices, electronics, etc. Some of the common applications of CNC machining include: Prototyping, Production, Customization, Repair and maintenance, Art and design. Overall, CNC machines provide a versatile and efficient manufacturing solution for a wide range of applications.
-
What is CNC machine examples?
CNC (Computer Numerical Control) machines are automated tools that can be programmed to perform precise tasks. Some common examples of CNC machines include: CNC milling machines, CNC lathes, CNC routers, CNC plasma cutters, CNC laser cutters. There are many other types of CNC machines, each designed for specific applications and industries.
-
What is CNC vs manual machining?
CNC (Computer Numerical Control) machining and manual machining are two methods of manufacturing parts.
Manual machining is the process of removing material from a workpiece using manual tools such as lathes, milling machines, drill presses, and grinders. This process requires skilled machinists who use their expertise to control the machinery and produce the desired outcome.
On the other hand, CNC machining utilizes computer-controlled machines to remove material from a workpiece. The machine is programmed with a set of instructions that control the movement of the cutting tools, allowing for precise and repeatable cuts. This process reduces the need for skilled operators and can be more efficient and accurate than manual machining.
Overall, CNC machining is ideal for producing large quantities of identical parts, while manual machining is better suited for smaller runs or custom jobs where specialized skills are required.
-
Why is CNC better than manual?
CNC (Computer Numerical Control) machines are generally considered to be better than manual machines for several reasons:
- Increased Precision: CNC machines can perform very precise cuts and movements, which is difficult or impossible to achieve with manual machines. This precision is due to the automation of the cutting process, which ensures that the machine moves exactly as programmed.
- Consistency: CNC machines can repeat the same cutting operations over and over again with consistent results. Manual machines, on the other hand, require a skilled operator who may not be able to maintain the same level of consistency over time.
- Speed: CNC machines can typically cut material much faster than manual machines, which can lead to increased productivity and reduced manufacturing costs.
- Reduced Labor Costs: CNC machines require less labor input than manual machines, as they can be operated by a single operator who can manage multiple machines at once.
Overall, the benefits of CNC machines make them a popular choice in modern manufacturing environments where efficiency, precision, and consistency are critical factors.
-
What is the difference between CNC machine and lathe machine?
A lathe machine is a type of manual machine that rotates a workpiece against a cutting tool to remove material, typically for shaping the workpiece into a cylindrical shape. A CNC machine, on the other hand, is a computer-controlled machine that automates the cutting and shaping process.
Some key differences between CNC machines and lathe machines include:
- Automation: CNC machines are fully automated and controlled by a computer program, while lathe machines require manual operation.
- Precision: CNC machines are capable of very precise cuts and movements, which is difficult or impossible to achieve with manual machines like lathes.
- Complexity: CNC machines can perform complex operations on a variety of materials, including metals, plastics, and composites, while lathes are typically used for simpler turning operations.
- Programming: CNC machines require programming and setup time, while lathes can be operated quickly with little preparation.
In summary, while both CNC machines and lathe machines are used for cutting and shaping materials, CNC machines offer greater precision, versatility, and automation. Lathe machines, on the other hand, are simpler to operate and can be more cost-effective for simpler turning operations.
-
What is the difference between CNC and non CNC?
The main difference between CNC (Computer Numerical Control) and non-CNC machines is in the way they are operated. CNC machines are automated and controlled by computer programs, while non-CNC machines require manual operation.
-
Is CNC the same as CAD?
No, CNC (Computer Numerical Control) is not the same as CAD (Computer-Aided Design).
CNC refers to the automation of the cutting and shaping process using computer programs. A CNC machine receives instructions from a computer program that tells it how to cut or shape the material based on a 3D model or other instructions.
On the other hand, CAD refers to the process of creating a digital 3D model of an object using specialized software. CAD software is used to design parts, products, buildings, and other objects in a virtual environment.
While CNC machines can be used to produce parts based on CAD models, they are not the same thing. CAD software is used to create the digital models that are then used to program the CNC machine to produce physical parts. In this way, CAD and CNC technologies work together to enable advanced manufacturing processes.
-
Is CNC a mill or lathe?
CNC (Computer Numerical Control) is not a specific type of machine, but rather a technology that can be applied to different types of machines, including mills and lathes.
CNC milling machines use rotary cutting tools to remove material from a workpiece and create complex shapes and designs. They are typically used for operations like drilling, cutting, and shaping.
CNC lathes, on the other hand, rotate a workpiece against a cutting tool to remove material and create a cylindrical shape. They are typically used for turning operations and can produce symmetrical parts like shafts and valves.
Both CNC milling machines and lathes can offer high levels of precision and automation, making them popular choices in modern manufacturing environments.
-
Is CNC machining a good skill?
Yes, CNC (Computer Numerical Control) machining is a highly valuable skill in today’s manufacturing industry.
CNC machines are widely used in various manufacturing industries such as aerospace, automotive, medical, electronics, and many more. The ability to operate and program CNC machines requires specialized technical skills and knowledge of programming languages like G-code, which are in high demand in the job market.
Having experience with CNC machining can lead to job opportunities as a CNC machine operator, CNC programmer, machinist, or manufacturing engineer, among others. These jobs typically offer competitive salaries and benefits.
Furthermore, as technology advances and industries continue to evolve, the demand for skilled CNC machinists is likely to increase. Therefore, learning CNC machining is an excellent career choice for individuals interested in pursuing a career in the manufacturing industry.
-
Why is it called CNC?
The term CNC stands for “Computer Numerical Control.” The name comes from the fact that CNC machines are controlled using a computer, which reads numerical code to dictate how the machine should move and cut the material.
CNC machines were first developed in the 1940s and 1950s as a way to automate the cutting process. They were initially used mostly for metalworking applications, but have since been adapted for use with a wide variety of materials, including plastics, wood, and composites.
The use of computers to control machine tools revolutionized the manufacturing industry by enabling greater precision, speed, and consistency in the production of parts and products. Today, CNC technology is widely used across various industries, from automotive and aerospace to healthcare and electronics.
-
What is the working principle of CNC?
CNC machines work by using computer programs to automate the cutting and shaping process. The process begins with designing a digital 3D model of the part or product that needs to be manufactured using CAD software. This model is then converted into a CNC program, which contains instructions for the machine on how to cut or shape the material, typically written in G-code. Once the material is secured to the worktable and the necessary cutting tools are loaded, the CNC program is executed, guiding the cutting tool across the material to create the desired shape. The finished part is then removed from the machine and any necessary finishing operations are performed. Overall, CNC machines offer a high degree of precision, accuracy, and consistency in manufacturing parts and products.
-
What technology is used in CNC machines?
CNC machines rely on a variety of technologies to automate the cutting and shaping process, including computer programming, servo motors, sensors and feedback systems, CAD/CAM software, G-code language, and tool changers. These technologies work together to allow CNC machines to perform a wide range of cutting and shaping operations with high precision and accuracy. CAD software is used to create digital models of parts or products, while CAM software generates the CNC program that controls the cutting operation. The G-code language is used to direct the movements and cutting operations of the machine. Servo motors power the machine’s axes, allowing for precise movement and cutting operations. Sensors and feedback systems monitor the cutting process and adjust the machine’s position and speed as needed, and tool changers allow for quick and easy swapping of cutting tools during the manufacturing process.
-
What language do CNC machines use?
CNC machines typically use a programming language called G-code (also known as RS-274 or EIA-274). G-code is a language that instructs the CNC machine how to move its tools to fabricate a part according to a set of coordinates and commands. These commands include instructions for tool movement, spindle speed, coolant flow, and other parameters necessary for the machining process.
-
Where is CNC machining used?
-
Is CNC a machine or software?
CNC (Computer Numerical Control) refers to a system that utilizes both hardware and software components to control and automate the operation of machines through numerical instructions. Therefore, CNC can refer to both a machine and software.
-
Is CNC machining easy?
CNC machining requires specialized knowledge and skills to operate, program, and maintain the machines properly. It may not be easy for those who do not have experience or training in this field. However, with proper training and practice, it could become easier to use CNC machines for various applications.
-
Is CNC only for metal?
CNC machines can be used to process a wide range of materials, including but not limited to metals. They can also cut and shape plastics, wood, composites, and other materials, depending on the type of machine and tools used.
-
What are 3 disadvantages of a CNC machine?
- High Initial Investment: CNC machines can be quite expensive, making them a significant initial investment that may not be feasible for all businesses.
- Require Skilled Operators: The operation of CNC machines requires specific technical skills and expertise, which may limit the number of qualified operators available.
- Limited Flexibility: While CNC machines are capable of producing high-quality and precise parts, they are limited in terms of flexibility because they require specific programming and tooling for each part. This means that they may not be suitable for small batch or custom production runs.
-
What are the 3 advantages of CNC machining?
The 3 advantages of CNC machining are:
One disadvantage of using a CNC machine is the initial cost, which can be much higher than traditional manual machines. Additionally, CNC machines require skilled operators to program and operate them effectively, which can result in higher labor costs. Finally, if a CNC machine breaks down, repairs can be more complex and expensive compared to traditional manual machines.
KYLT CNC Machining Services:
Home>CNC Machining Services>CNC Milling Services
Home>CNC Machining Services>CNC Turning Services
Home>CNC Machining Services>Rapid Prototyping Services
Home>CNC Machining Services>Injection Molding Services
KYLT CNC Precision Machined Parts:
Home>Precision CNC Machined Parts
Home>Precision CNC Machined Parts>CNC Precise Turned Parts
Home>Precision CNC Machined Parts>CNC Precise Milled Parts
Home>Precision CNC Machined Parts>Aluminum Machining
Home>Precision CNC Machined Parts>Magnesium Machining
Home>Precision CNC Machined Parts>Copper & Brass Machining
Home>Precision CNC Machined Parts>Steel Machining
Home>Precision CNC Machined Parts>Stainless Steel Machining
Home>Precision CNC Machined Parts>Plastic Machining
More information about Machining Technology: