Zinc die casting parts or Zamak die casting parts is the process of manufacturing high-volume, net-shaped components made from ZINC/ZAMAK alloys. The process involves melting the zinc/zamak alloy and injecting it into a customized die to create the desired shape. The molten metal quickly solidifies, allowing for the rapid production of small to medium-sized parts with excellent accuracy and surface finish. Zinc/Zamak alloys are known for their strength, durability, and resistance to corrosion, making them ideal for a wide range of applications in industries such as automotive, electronics, and consumer products.
KYLT, is one of the Zinc/Zamak die casting parts suppliers and die-casting parts manufacturers. Provide small and big size Zinc/Zamak die casting services with Cold chamber die casting machines and Hot chamber die casting machines.
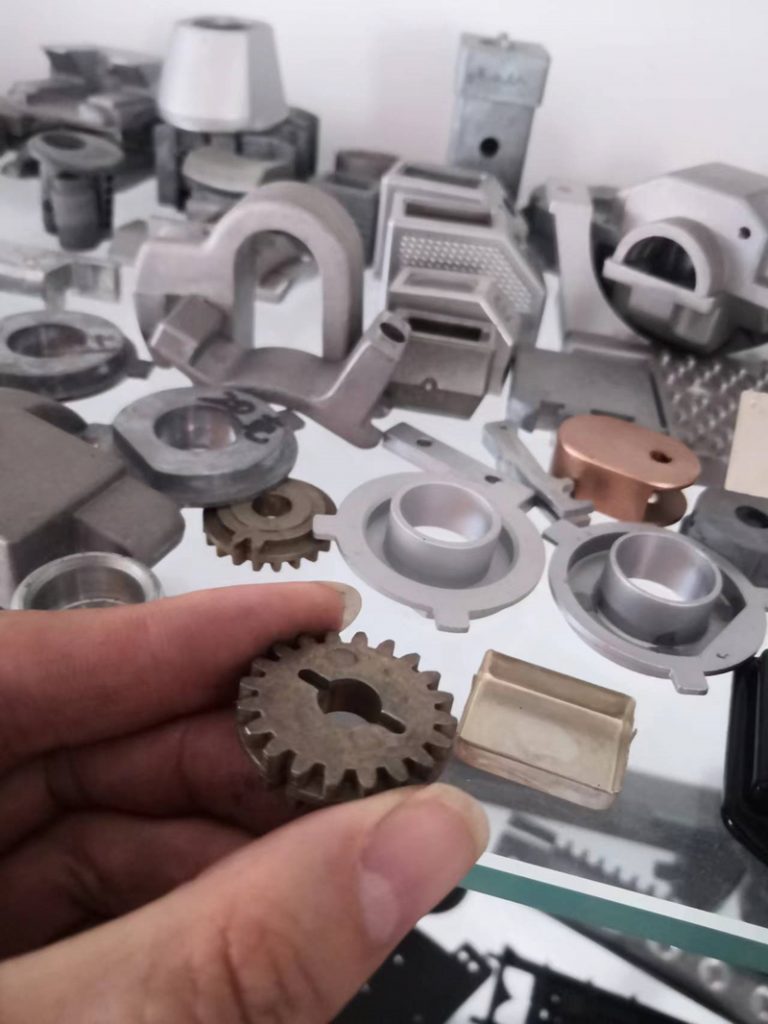
Zinc Die Casting Parts: Why They’re an Essential Component for Many Industries
Meta Description: Discover the importance of Zamak/Zinc die casting parts in various industries and how they can benefit your business.
Introduction
When it comes to manufacturing components for various industries, one material that has become increasingly popular is zinc. This versatile metal can be used to create a wide range of products, from small parts for electronic devices to larger components for machinery and automobiles. One of the most popular methods of producing zinc parts is through die casting, which involves melting the metal and injecting it into a mold to create the desired shape.
Zinc/Zamak die casting parts have become an essential component in many industries due to their durability, strength, and versatility. In this article, we’ll take a closer look at why zinc die casting parts are so popular and the benefits they offer to businesses.
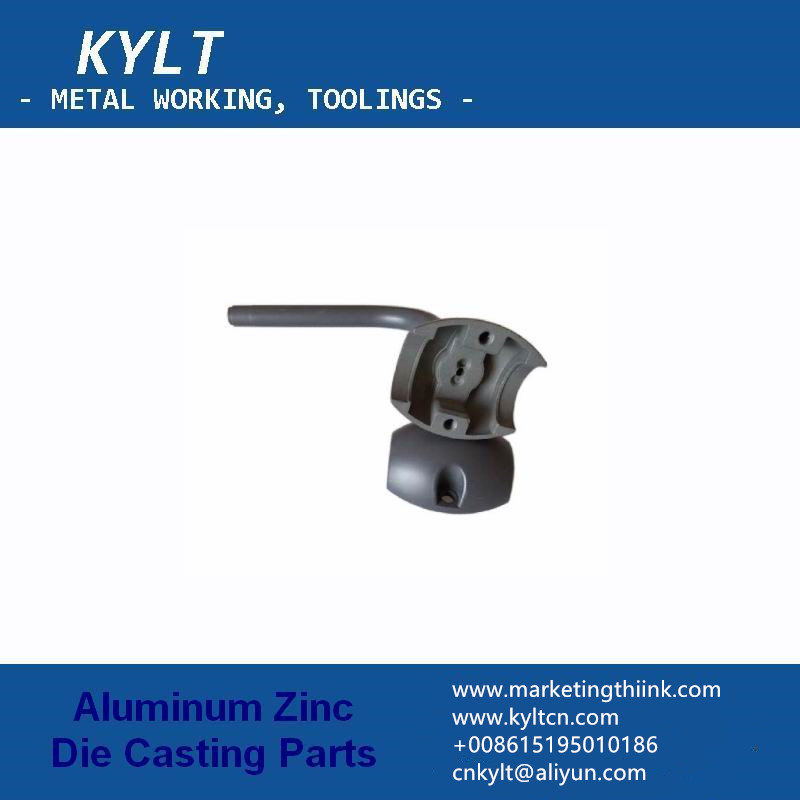
Machining methods of zinc die casting parts
Zinc die casting parts can be machined using a variety of methods, depending on the specific requirements of the application. Some of the commonly used machining methods include:
- CNC Machining: This method involves the use of computer-controlled machines to create precise and complex shapes in the Zamak/Zinc die casting parts. CNC machining offers high accuracy and repeatability, making it ideal for producing large quantities of consistent parts.
- Drilling: This method involves using a drill bit to create holes in the zinc die casting parts. Drilling can be used to create holes of various sizes and shapes in the parts.
- Milling: This method involves using a milling machine to cut and shape the surface of the Zamak/Zinc die casting parts. Milling can be used to create complex shapes and contours in the parts.
- Turning: This method involves rotating the Zamak/Zinc die casting parts against a cutting tool to remove material and create a desired shape. Turning can be used to create cylindrical shapes such as shafts and pins.
- Grinding: This method involves using an abrasive wheel or belt to remove material from the surface of the Zamak die-casting part. Grinding can be used to create a smooth and polished surface finish on the parts.
The choice of machining method will depend on the specific requirements of the part, including factors such as accuracy, complexity, and surface finish.
Now, KYLT provides Zamak die casting parts‘ machining methods are CNC milling, NC turning, Drilling, Tapping, and Grinding. As per different machining requirements of parts, we make machining jigs and fixtures. Also, we design and make checking tools for the machined parts’ quality inspection.
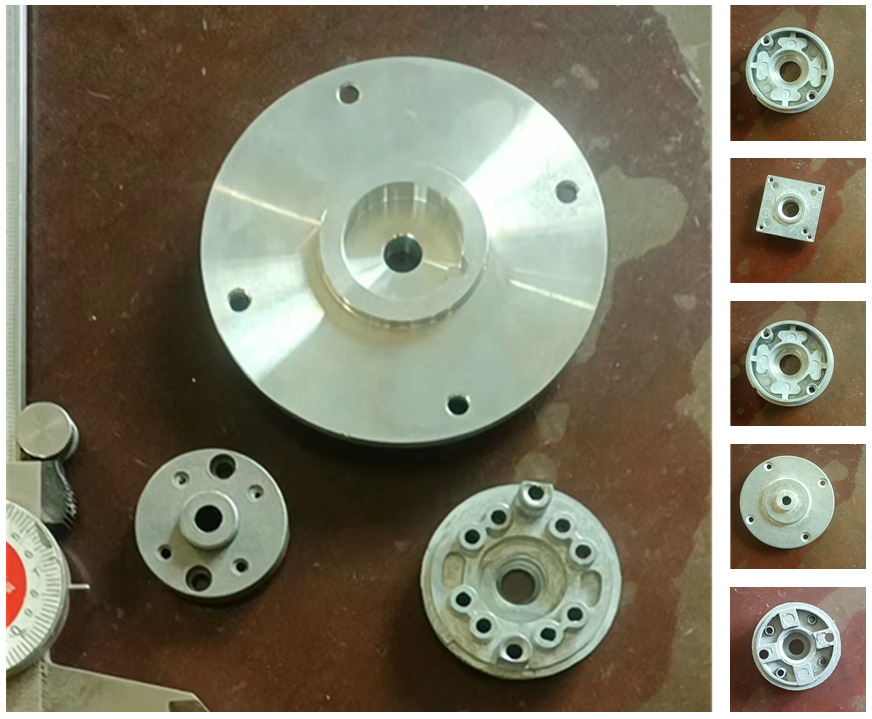
KYLT Precision CNC machining services (milling & turning service), Fast prototyping, Fixture/Jig/Tooling making, Aluminum/Zinc Zamak die casting & plastic injection parts. Email:cnkylt@aliyun.com
Surface treatment methods of zinc die casting parts
There are various surface treatment methods available for Zamak die casting parts. Some of the commonly used methods include:
- Shot blasting: it is a surface treatment process in which abrasive particles, such as steel shots or grits, are propelled at high velocity against a metal surface using compressed air. The impact of these particles on the surface removes impurities, rust, scales, and other surface contaminants, leaving behind a clean and textured surface. Shot blasting is commonly used in various industries, including automotive, aerospace, construction, and metalworking, for applications such as preparing surfaces for painting, cleaning and deburring castings, and improving the fatigue life of metal components.
- Vibration grinding: also known as vibratory finishing, is a surface finishing process in which abrasive particles are fed into a vibrating bowl or tub along with workpieces and a liquid compound. The vibration of the bowl causes the abrasive particles to move around and come into contact with the workpieces, removing sharp edges, burrs, and other imperfections on the surface. The liquid compound acts as a lubricant and helps the abrasive particles to achieve a uniform finish on the surface.
- Polishing: it is a surface finishing process used to improve the appearance and properties of a material’s surface. The process involves using an abrasive material, such as a polishing compound or polishing wheel, to remove small amounts of material from the surface of the workpiece.
- Electroplating: This method involves coating the ZAMAK die casting parts with a thin layer of another metal such as chrome, nickel or gold, to improve their corrosion resistance and aesthetic appearance.
- Powder Coating: This process involves applying a dry powder onto the surface of the ZINC die casting parts, which is then heated to fuse the powder into a protective coating that provides improved durability and resistance to abrasion.
- Anodizing: This method involves altering the surface of the ZAMAK die-casting parts through an electrochemical process to form a hard, durable oxide layer that improves their resistance to wear and tear, as well as corrosion.
- Painting: ZINC die casting parts can be painted with a variety of coatings to improve their appearance, as well as protect them from environmental factors such as moisture, sunlight, and heat.
- Chemical Treatment: This method involves treating the surface of the zinc die casting parts with chemicals such as phosphates or chromates, to create a protective layer that enhances their resistance to corrosion.
The choice of surface treatment method will depend on the specific requirements of the application, including factors such as durability, appearance, and resistance to environmental factors.
Now, in KYLT Zamak die casting services, we can quote for the surface treatment of Shot blasting, Vibration grinding, Polishing, Electroplating, Powder coating, and Painting.
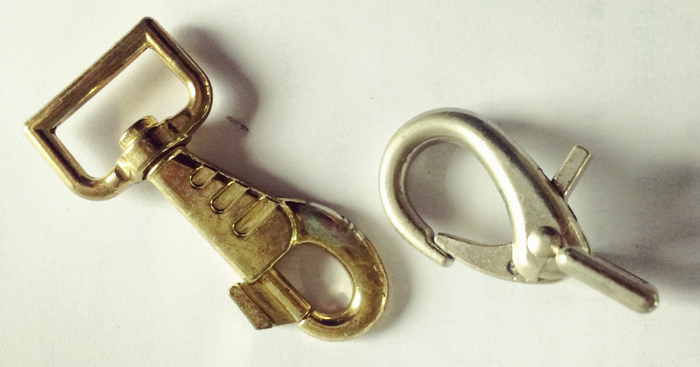
Advantages of Zinc Zamak Die Casting Parts
There are many reasons why zinc die casting parts have become so popular in various industries. Some of the advantages of using zinc die casting parts include:
1. Cost-Effective
One of the main advantages of using zinc die casting parts is their cost-effectiveness. Compared to other materials like aluminum or stainless steel, zinc is a relatively inexpensive material. Additionally, the die casting process is very efficient and can produce large quantities of parts quickly and at a lower cost.
2. High Strength-to-Weight Ratio
Despite its low cost, zinc is a strong and durable material. In fact, it has one of the highest strength-to-weight ratios of all metals, making it ideal for creating components that need to be both strong and lightweight.
3. Versatility
Zinc die casting parts can be used to create a wide range of components in various shapes and sizes. This versatility makes it a popular choice for industries like automotive, aerospace, and electronics.
4. Excellent Corrosion Resistance
Zinc is naturally resistant to corrosion, making it an ideal material for parts that will be exposed to harsh environments. This resistance to corrosion helps to extend the life of the parts and reduce maintenance costs over time.
5. Dimensional Accuracy
Zinc die casting parts are known for their dimensional accuracy, which means they can be manufactured to exact specifications. This accuracy ensures that the parts fit together perfectly and work as intended, which is essential for critical components like those used in the automotive and aerospace industries.
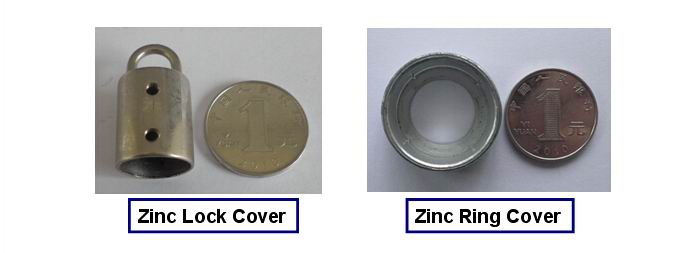
Applications of Zinc/Zamak Die Casting Parts
Zinc/Zamak die casting parts have a wide range of applications across various industries. Some of the most common applications include:
1. Automotive Industry
Zamak die casting parts are widely used in the automotive industry to create components like brackets, gears, and housings. Due to their strength and durability, zinc parts can withstand the harsh conditions of automotive environments and last for many years.
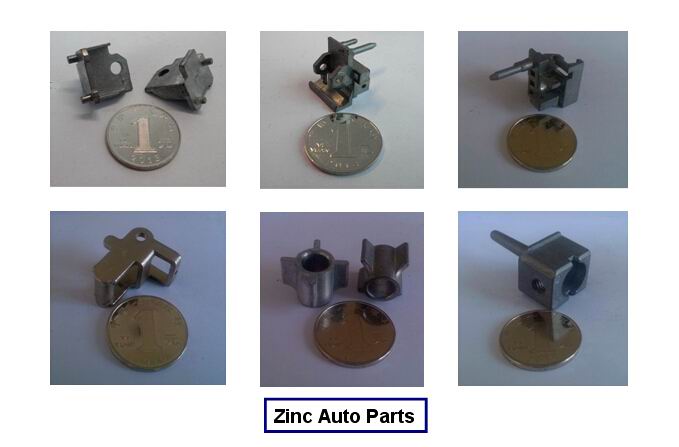
2. Electronics Industry
The electronics industry also relies heavily on zinc die casting parts to create components like connectors, switches, and brackets. The versatility and dimensional accuracy of zinc parts make them ideal for use in electronic devices.
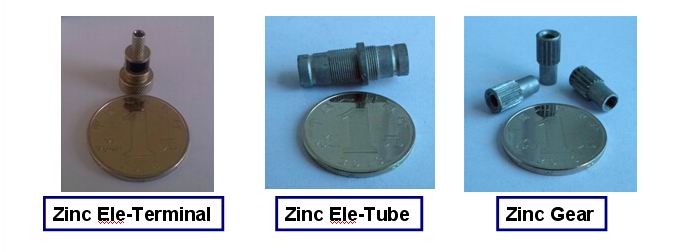
3. HOUSEHOLD APPLIANCE, fURNITURE Industry
In the household appliance & furniture industry, zinc die casting parts are used to create components like connectors, door handles, gears, gearboxes, and housing or covers. Zinc die casting parts are commonly used in household appliances due to their durability, strength, and resistance to corrosion.
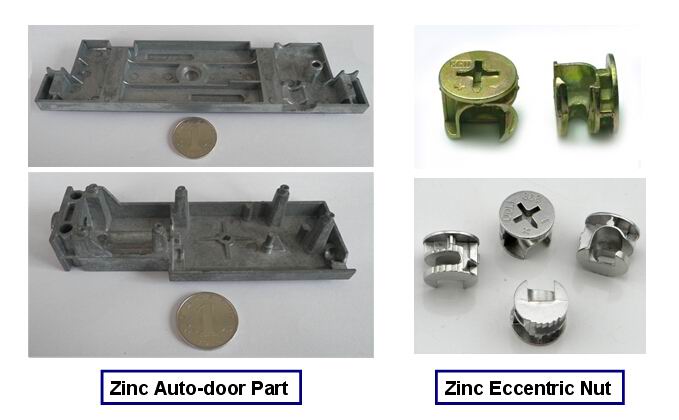
4. Construction Industry
Zinc die casting parts are also used in the construction industry to create components like door handles, locks, and hinges. The corrosion resistance of zinc makes it ideal for use in outdoor environments where the parts may be exposed to moisture and other harsh conditions.
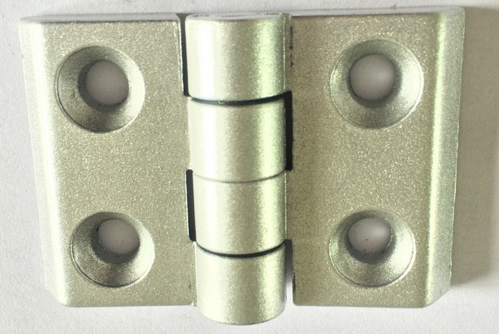
5. CLOTHING, LUGGAGE & JEWELRY Industry
Zinc/Zamak die casting parts are commonly used in the manufacturing of clothing, luggage, and jewelry.
In clothing, zinc die casting parts can be found in various types of hardware such as buttons, zippers, buckles, and clasps.
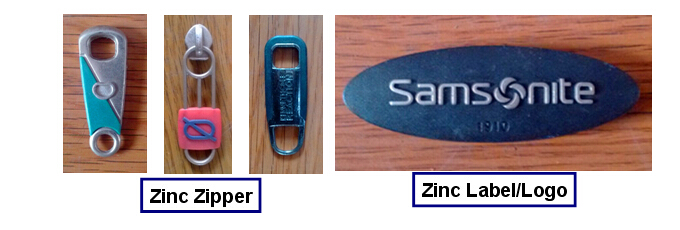
In luggage, Zamak/Zinc die casting parts are used in locks, hinges, handles, and other hardware components.
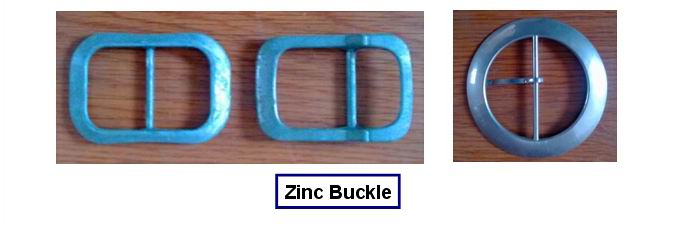
In jewelry, zinc die casting parts are used in the production of clasps, chains, pendants, and other decorative elements.
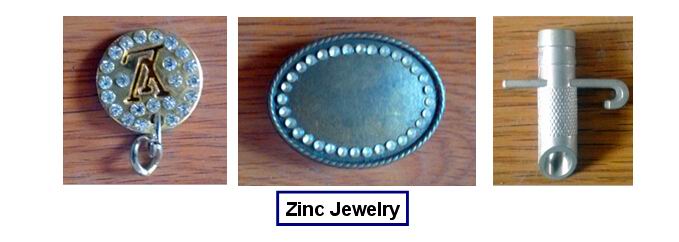
Get a FREE quote of Zamak Zinc Zn. alloy die casting mold and die casting parts service, please email us: cnkylt@aliyun.com
Zamak Die Casting and Zinc Die Casting: What’s the Difference?
Zinc die casting and zamak die casting are two popular methods of manufacturing metal parts. Both methods use the same base material, zinc, but there are some key differences between the two processes. In this article, we’ll explore the similarities and differences between zinc die casting and zamak die casting.
Introduction
Die casting is a process that involves forcing molten metal into a mold cavity at high pressure. The metal then solidifies and takes on the shape of the mold. This process is used to create a wide range of metal parts with complex shapes and sizes. Zinc is a popular material for die casting due to its low melting point, excellent fluidity, and ability to be easily shaped and molded.
Zinc Die Casting
Zinc die casting is a manufacturing process that involves melting zinc and forcing it into a mold at high pressure. The result is a strong, durable, and lightweight metal part that can be easily machined, finished, and coated.
One of the key advantages of zinc die casting is its cost-effectiveness. Zinc is a highly abundant material, which makes it relatively inexpensive compared to other metals. Additionally, the die casting process itself is highly efficient and generates very little waste.
Zinc die casting is also highly versatile and can be used to create a wide range of metal parts in various shapes and sizes. From automotive components to electronic enclosures, zinc die casting parts have a wide range of applications.
Zamak Die Casting
Zamak is a type of zinc alloy that is specifically designed for die casting applications. The name “zamak” is derived from the German word “Zink,” which means zinc, and the acronym for the alloys that make up the material: Zn-Al-Mg-Ku.
Zamak die casting is a manufacturing process that involves melting the zamak alloy and forcing it into a mold at high pressure. The result is a strong, durable, and lightweight metal part that can be easily machined, finished, and coated.
One of the key advantages of zamak die casting is its high strength and durability. Zamak alloys are known for their excellent mechanical properties, including high tensile strength, corrosion resistance, and wear resistance.
Zamak die casting is also highly versatile and can be used to create a wide range of metal parts in various shapes and sizes. From automotive components to household appliances, zamak die casting parts have a wide range of applications.
The Differences Between Zinc Die Casting and Zamak Die Casting
While both zinc die casting and zamak die casting use the same base material, there are some key differences between the two processes:
Alloy Composition
Zinc die casting can be done using a variety of zinc alloys, including ZA-8, ZA-12, and ZA-27. These alloys contain varying amounts of aluminum, copper, and magnesium, which can affect the final properties of the part.
Zamak die casting, on the other hand, uses a specific alloy (Zn-Al-Mg-Ku) that is designed for die casting applications. This alloy has a consistent composition, which ensures consistent mechanical properties across all parts.
Mechanical Properties
Zamak alloys are known for their excellent mechanical properties, including high strength, corrosion resistance, and wear resistance. While zinc alloys used in zinc die casting can also have good mechanical properties, they may not be as strong or durable as zamak alloys.
Surface Finish
Zamak alloys have a smooth surface finish that is ideal for applications where a high-quality surface is required, such as automotive components or household appliances. Zinc alloys used in zinc die casting may have a slightly rougher surface finish, which may require additional machining8888888
Advantages of Zinc and Zamak Die Casting Parts
Both zinc and zamak die casting parts have a range of advantages over other manufacturing methods, including:
Strength and Durability
Zinc and zamak die casting parts are known for their high strength and durability. This makes them ideal for applications that require parts that can withstand high stress and wear.
Versatility
Both zinc and zamak die casting parts can be easily shaped and molded into a wide range of complex shapes and sizes. This makes them ideal for applications that require customized parts with unique shapes and designs.
Cost-effectiveness
Zinc and zamak die casting parts are highly cost-effective due to the low cost of the materials and the efficiency of the die casting process. This makes them an ideal choice for mass production applications where cost is a key factor.
Surface Finish
Zamak alloys have a smooth surface finish that is ideal for applications where a high-quality surface is required. Zinc alloys used in zinc die casting may have a slightly rougher surface finish, but can still be easily machined and finished.
Conclusion
Zinc and zamak die casting are two popular methods of manufacturing metal parts. Both methods use the same base material, zinc, but there are some key differences between the two processes. Zinc die casting is cost-effective and versatile, while zamak die casting is known for its high strength and durability. Both zinc and zamak die casting parts have a range of advantages over other manufacturing methods, including strength and durability, versatility, cost-effectiveness, and surface finish. With their wide range of applications, zinc and zamak die casting parts are an important part of the manufacturing industry.
Conclusion
Yes, zinc die casting parts are considered to be environmentally friendly. Zinc is a highly recyclable material, and the die casting process generates very little waste. Additionally, zinc parts have a long lifespan and require minimal maintenance, which reduces the need for replacement and reduces waste over time.
If you’re looking for a reliable and cost-effective material for your next manufacturing project, consider using zinc die casting parts. With their many advantages and applications, zinc zamak parts can help your business save money, improve performance, and reduce maintenance costs over time.
KYLT Provides Zinc/Zamak/Zn. Die casting mold & parts service, Provides Precision CNC machining services (milling & turning service), Fast prototyping, Fixture/Jig/Tooling making, Aluminum die casting services. Email: cnkylt@aliyun.com
Frequently Asked Questions about Zinc Die Casting Parts
What is the difference between zinc die casting and zamak die casting?
The main difference between zinc die casting and zamak die casting is the alloy composition. Zinc die casting can use a variety of zinc alloys, while zamak die casting uses a specific alloy (Zn-Al-Mg-Ku) that is designed for die casting applications.
What are the advantages of zinc and zamak die casting parts?
Zinc and zamak die casting parts are known for their high strength and durability, versatility, cost-effectiveness, and smooth surface finish.
What applications are zinc and zamak die casting parts used for?
Zinc and zamak die casting parts have a wide range of applications, including automotive components, household appliances, electronics, hardware, and more.
What is the difference between zinc die casting and aluminum
Zinc and aluminum are both popular materials used in die casting. However, zinc has a lower melting point and is more ductile, which means it can be easily shaped and molded into complex designs. Zinc is also more cost-effective compared to aluminum. On the other hand, aluminum is known for its high strength and resistance to heat, making it ideal for components that require durability and stability in high-temperature environments.
Are zinc die casting parts environmentally friendly?
Zamak/Zinc die casting parts have become an essential component in various industries due to their cost-effectiveness, strength, versatility, and excellent corrosion resistance. From automotive to aerospace, electronics to construction, zinc die casting parts have a wide range of applications and can be used to create a wide range of components in various shapes and sizes.
Can zinc die casting parts be painted or coated?
Yes, zinc/zamak die casting parts can be painted or coated with a variety of materials to enhance their appearance or improve their functionality. Zinc is a highly receptive material, which means it can be easily coated with a wide range of materials, including paints, platings, and anodized coatings.
KYLT CNC Machining Services:
Home>CNC Machining Services>CNC Milling Services
Home>CNC Machining Services>CNC Turning Services
Home>CNC Machining Services>Rapid Prototyping Services
Home>CNC Machining Services>Injection Molding Services
KYLT CNC Precision Machined Parts:
Home>Precision CNC Machined Parts
Home>Precision CNC Machined Parts>CNC Precise Turned Parts
Home>Precision CNC Machined Parts>CNC Precise Milled Parts
Home>Precision CNC Machined Parts>Aluminum Machining
Home>Precision CNC Machined Parts>Magnesium Machining
Home>Precision CNC Machined Parts>Copper & Brass Machining
Home>Precision CNC Machined Parts>Steel Machining
Home>Precision CNC Machined Parts>Stainless Steel Machining
Home>Precision CNC Machined Parts>Plastic Machining
More information about Machining Technology: