Introduction
Spiral Desiccant Closures (desiccant cap closure) manufacturing service, from mold making to plastic molding, is a comprehensive solution that caters to the specific needs of companies in various industries. These closures play a crucial role in preserving the freshness and quality of products by effectively sealing containers and preventing moisture ingress. This article delves into the intricacies of the manufacturing process, highlighting the importance of mold making and plastic molding in the production of Spiral Desiccant Closures.
KYLT provides no-standard PE, PP material Spiral Desiccant Closures making service, from mold making to plastic injection molding.
Service email: cnkylt@aliyun.com
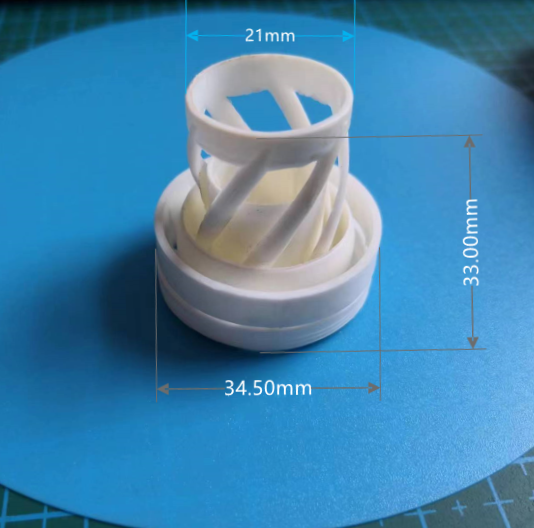
The Significance of Spiral Desiccant Closures
Spiral Desiccant Closures have gained immense popularity due to their exceptional moisture absorption properties and efficient sealing capabilities. They are widely used in industries such as pharmaceuticals, food and beverages, electronics, and more. These closures ensure the integrity of the packaged products by safeguarding them against moisture damage, thus extending their shelf life and maintaining their overall quality.
Understanding Mold Making for Spiral Desiccant Closures
Mold-making forms the foundation of the manufacturing process for Spiral Desiccant Closures. It involves the creation of precise and durable molds that are used to shape the closures. The mold-making process requires expertise and attention to detail to ensure that the final product meets the desired specifications. Advanced technologies like Computer-Aided Design (CAD) and Computer-Aided Manufacturing (CAM) are often employed to streamline the mold-making process and enhance precision.
KYLT provides no-standard PE, PP material Spiral Desiccant Closures making service, from mold making to plastic injection molding.
Service email: cnkylt@aliyun.com
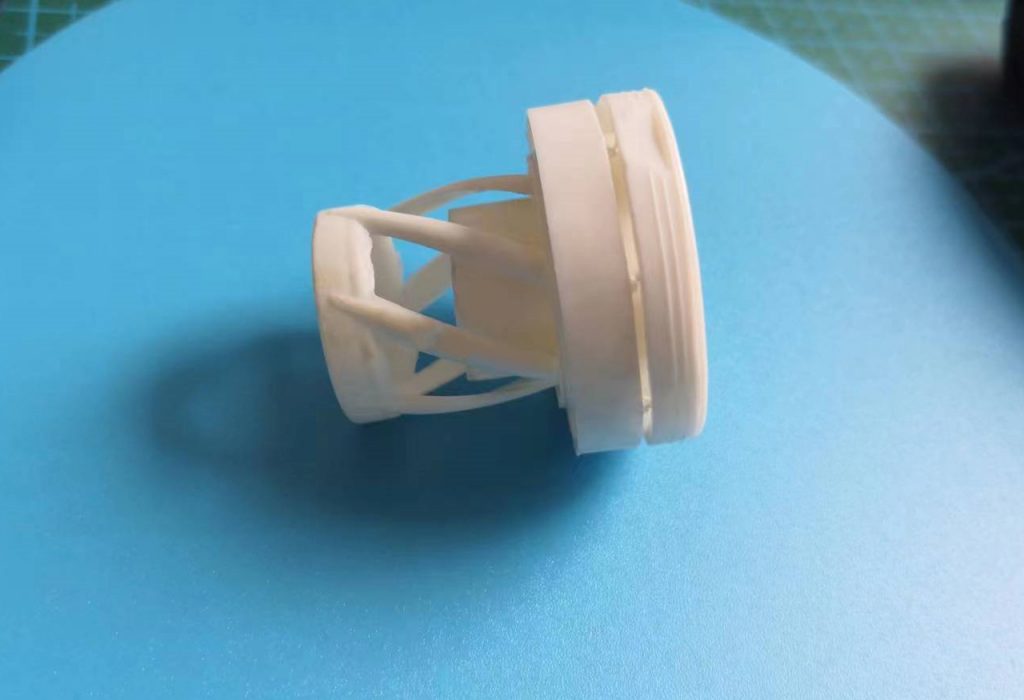
Plastic Molding Techniques for Spiral Desiccant Closures
Plastic molding is a key step in the manufacturing of Spiral Desiccant Closures. This process involves injecting molten plastic material into the mold cavity, allowing it to cool and solidify into the desired shape. Various plastic molding techniques, such as injection molding, blow molding, and rotational molding, can be employed based on the specific requirements of the closures.
Injection Molding: Efficient and Precise
Injection molding is the most commonly used technique for manufacturing Spiral Desiccant Closures. It offers numerous advantages, including high production rates, consistent quality, and intricate design possibilities. In this process, molten plastic is injected into the mold under high pressure, ensuring precise and detailed replication of the mold’s shape. The result is a durable and reliable closure that effectively seals the container.
Blow Molding: Ideal for Hollow Closures
Blow molding is a suitable technique for producing hollow Spiral Desiccant Closures. It involves the inflation of a heated plastic parison inside a mold, which then takes the shape of the mold as it cools down. This technique allows for the creation of lightweight closures with excellent sealing properties. Blow molding is particularly useful for large-scale production of closures, as it offers cost-effectiveness and high productivity.
Rotational Molding: Versatile and Durable
Rotational molding, also known as roto-molding, is a versatile technique employed for manufacturing complex-shaped Spiral Desiccant Closures. It involves the rotation of a mold around multiple axes while the plastic material inside the mold gradually coats its interior surface. This process ensures uniform thickness and strength throughout the closure. Rotational molding offers design flexibility, excellent impact resistance, and the ability to incorporate additional features such as handles or tamper-evident elements.
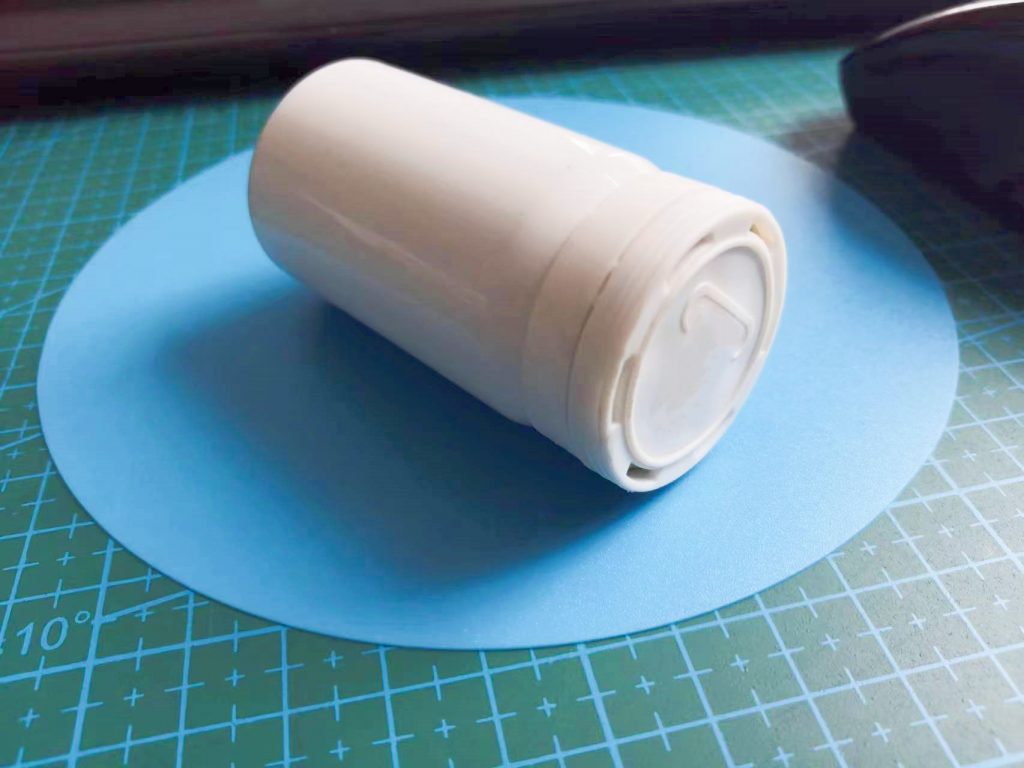
We only provide injection molding methods to produce no-standard PE, PP material Spiral Desiccant Closures.
For desiccant cap closures’ price, mold design and making services, please email: cnkylt@aliyun.com
Conclusion
Spiral Desiccant Closures (desiccant cap closure) manufacturing service, from mold making to plastic molding, is a comprehensive solution that caters to industries requiring efficient moisture protection and sealing capabilities. The mold-making process and plastic molding techniques play pivotal roles in producing high-quality closures that preserve the freshness and integrity of various products.
Companies can make informed decisions about their manufacturing processes by understanding the significance of mold making and the various plastic molding techniques available. Outsourcing the manufacturing service offers advantages such as expertise, cost savings, and scalability. Implementing rigorous quality control measures ensures that the closures meet stringent standards and provide reliable performance.
As the demand for Spiral Desiccant Closures continues to rise across industries, investing in a reliable manufacturing service that covers the entire process from mold making to plastic molding is crucial. By partnering with experienced manufacturers, companies can ensure the production of superior-quality closures that effectively protect their products from moisture damage.
KYLT provides FREE quotation for the price of mold and parts of Custom color high quality plastic child-proof bottle cap spiral covers,
Customized color with moisture-proof beads PE PP Plastic spring caps, PP Plastic Injection Desiccant Cap effervescent tablet bottle lid Plastic Caps For Bottles, Childproof spiral cap Child effervescent tablet tube cap CRC cap, Spring caps used for effervescent tablets tube, Cushioning spring caps will silica gel desiccant caps, Healthcare supplement Effervescent tablets tube spring lid and silica gel desiccant stopper, Cap for effervescent tube bottle plastic moisture-proof bottle cap silica gel desiccant closures.
For more information, please email us: cnkylt@aliyun.com
FAQs about Spiral Desiccant Closures Manufacturing Service
1. What are the benefits of Spiral Desiccant Closures?
Spiral Desiccant Closures offer numerous benefits, including:
- Effective moisture absorption, preserving product freshness.
- Enhanced shelf life and extended product quality.
- Reliable sealing, preventing leakage and contamination.
- Versatility in design and customization options.
- Compatibility with various container types.
2. How are the molds created for Spiral Desiccant Closures?
The molds for Spiral Desiccant Closures are created through a meticulous process that involves several steps:
- Design: The mold-making process begins with the design phase, where skilled engineers utilize advanced CAD software to create a 3D model of the desired closure. This step allows for precise measurements, intricate detailing, and the incorporation of specific features.
- Material Selection: Once the design is finalized, the appropriate materials for mold construction are selected. Common choices include steel and aluminum, known for their durability and resistance to high temperatures and pressures.
- Mold Fabrication: Skilled mold makers use the design specifications to fabricate the mold. This step may involve cutting, milling, grinding, and drilling the chosen material to achieve the desired shape and dimensions.
- Surface Treatment: To ensure optimal performance and longevity, the mold’s surfaces undergo surface treatment processes such as polishing, etching, or coating. These treatments enhance the mold’s smoothness, release properties, and resistance to wear and tear.
- Testing and Refinement: Once the mold is complete, it undergoes rigorous testing to ensure its functionality and accuracy. Any necessary adjustments or modifications are made to achieve the desired outcome.
- Production: With a finalized mold, the manufacturing process can commence. The mold is securely mounted onto an injection molding machine, and molten plastic material is injected into the mold cavity under controlled conditions, allowing the closure to take shape.
3. What factors should be considered during plastic molding for Spiral Desiccant Closures?
Several factors are crucial during plastic molding for Spiral Desiccant Closures:
- Material Selection: The choice of plastic material depends on various factors, such as the product’s compatibility, desired properties (such as strength or flexibility), and environmental considerations. Common materials include polypropylene (PP) and polyethylene (PE) due to their moisture resistance and durability.
- Quality Control: Throughout the plastic molding process, quality control measures are essential to ensure that the closures meet the required specifications. Regular inspections, dimensional checks, and testing for leakage or deformation help maintain consistent quality.
- Efficiency and Productivity: Plastic molding techniques should be selected based on the required production volume and efficiency. Injection molding is often preferred for high-volume production, while blow molding or rotational molding may be more suitable for specific closure designs or lower production quantities.
- Sustainability: In today’s environmentally conscious world, sustainable manufacturing practices are crucial. Consideration should be given to using recyclable materials, reducing waste, and implementing energy-efficient processes during plastic molding.
4. Can Spiral Desiccant Closures be customized to fit specific container sizes?
Yes, Spiral Desiccant Closures can be customized to fit a wide range of container sizes. The mold design process allows for the adaptation of closure dimensions, ensuring a perfect fit for different container types. Additionally, closures can be customized with features such as tamper-evident seals, handles, or branding elements to meet specific customer requirements.
5. What are the advantages of outsourcing Spiral Desiccant Closures manufacturing service?
Outsourcing Spiral Desiccant Closures manufacturing service offers several benefits:
- Expertise and Experience: Professional manufacturers specialize in the production of closures, bringing extensive knowledge and experience to ensure high-quality results.
- Cost Savings: Outsourcing eliminates the need for in-house mold-making and plastic molding infrastructure, reducing capital investment and overhead costs.
- Time Efficiency: By leveraging the expertise of a dedicated manufacturer, companies can streamline the production process, allowing them to focus on their core business activities.
- Scalability: Outsourcing enables companies to scale production volumes according to market demands without the burden of expanding their own.
6. What quality control measures are implemented during Spiral Desiccant Closures manufacturing?
Quality control is of utmost importance during Spiral Desiccant Closures manufacturing to ensure that the final product meets the highest standards. Here are some common quality control measures implemented:
- Raw Material Inspection: The quality of the plastic material used in the molding process is checked for consistency, purity, and compliance with industry standards.
- Mold Inspection: Molds undergo regular inspections to ensure their structural integrity, dimensional accuracy, and proper functioning.
- In-process Checks: During the molding process, frequent checks are conducted to monitor key parameters such as temperature, pressure, and cycle times to maintain consistency and prevent defects.
- Visual Inspection: Each manufactured closure undergoes visual inspection to identify any surface imperfections, color variations, or deformities.
- Performance Testing: Functional tests are performed to verify the closure’s sealing effectiveness, moisture absorption properties, and overall performance under different conditions.
- Packaging Inspection: The final packaged closures are inspected to ensure proper labeling, packaging integrity, and compliance with shipping standards.
KYLT CNC Machining Services:
Home>CNC Machining Services>CNC Milling Services
Home>CNC Machining Services>CNC Turning Services
Home>CNC Machining Services>Rapid Prototyping Services
Home>CNC Machining Services>Injection Molding Services
KYLT CNC Precision Machined Parts:
Home>Precision CNC Machined Parts
Home>Precision CNC Machined Parts>CNC Precise Turned Parts
Home>Precision CNC Machined Parts>CNC Precise Milled Parts
Home>Precision CNC Machined Parts>Aluminum Machining
Home>Precision CNC Machined Parts>Magnesium Machining
Home>Precision CNC Machined Parts>Copper & Brass Machining
Home>Precision CNC Machined Parts>Steel Machining
Home>Precision CNC Machined Parts>Stainless Steel Machining
Home>Precision CNC Machined Parts>Plastic Machining
More information about Machining Technology: