Use common type tap, which problems are always happen?
The main problems often occur in tapping process:
- Taper broken;
- Taper broken teeth;
- Tap wear is too fast;
- Excessive thread diameter;
- Too small thread diameter;
- Surface roughness of threads is too high.
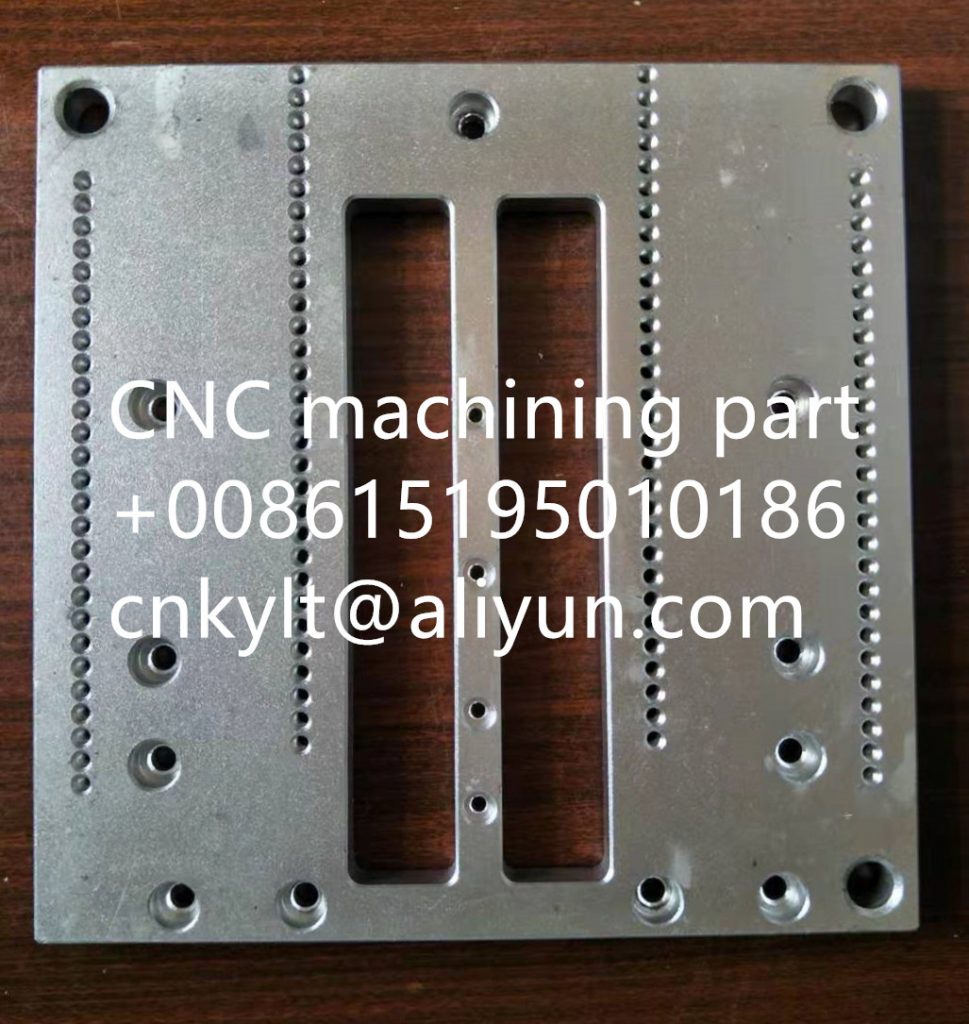
What cause the tapping problems happen in machining work?
1) Tap breakage
The diameter of the bottom hole is small and the chip removal is not good, which results in chip blockage; the depth of the drill hole is not enough when the thread can not be tapped; the cutting speed is too high and too fast when tapping thread; the diameter of the tap used for tapping thread is different from that of the bottom hole of thread; the selection of the grinding parameters of the tap is inappropriate, and the hardness of the workpiece is unstable; the tap is used for too long and wears excessively.
2) Tap thread broken
The front angle of the tap is too large; the cutting thickness of each tooth of the tap is too large; the quenching hardness of the tap is too high; the tap is used for too long and wears seriously.
3) Tap wears too fast
When tapping threads, the cutting speed is too high; the parameters of tap grinding are not appropriate; the cutting fluid is not selected properly and the cutting fluid is not enough; the material hardness of the workpiece is too high; the burns occur when tap grinding.
4) Excessive thread diameter
Improper selection of taper diameter accuracy grade; unreasonable cutting choice; too high cutting speed of tapping thread; poor coaxiality between taper and workpiece thread bottom hole; inappropriate selection of taper grinding parameters; burrs in tap grinding and too short length of tap cutting taper.
5) Thread diameter too small
Improper selection of taper diameter accuracy grade, unreasonable selection of taper grinding parameters, taper wear, and inappropriate selection of cutting fluid.
6) Excessive Surface Roughness of Thread
The selection of grinding parameters of tap is not appropriate; the hardness of workpiece material is too low; the grinding quality of tap is not good; the selection of cutting fluid is unreasonable; the cutting speed is too high when tapping threads; the use time of tap is too long and the wear is too large.
How to solve the tapping problems in machining process?
1) Choose the diameter of the bottom hole of the thread correctly when the tap breaks; the inclination angle of the edge grinding or the selection of spiral groove tap; the depth of the bottom hole should meet the specified standard; reduce the cutting speed appropriately and select according to the standard; correct the tap and the bottom hole when tapping the thread to ensure that its coaxiality meets the requirements, and select floating tapping chuck; increase the front angle of the tap to shorten the length of the cutting taper; and ensure the workpiece. Hardness meets the requirements and safety chuck is selected.
2) The breaking teeth of the tap should be reduced properly; the length of the cutting taper should be increased properly; the hardness should be reduced and the tap should be replaced in time.
3) Too fast wear of the tap reduces the cutting speed properly; reduces the front angle of the tap, lengthens the length of the cutting taper; chooses the cutting fluid with good lubricity; carries on the appropriate heat treatment to the processed parts; correctly grinds the tap.
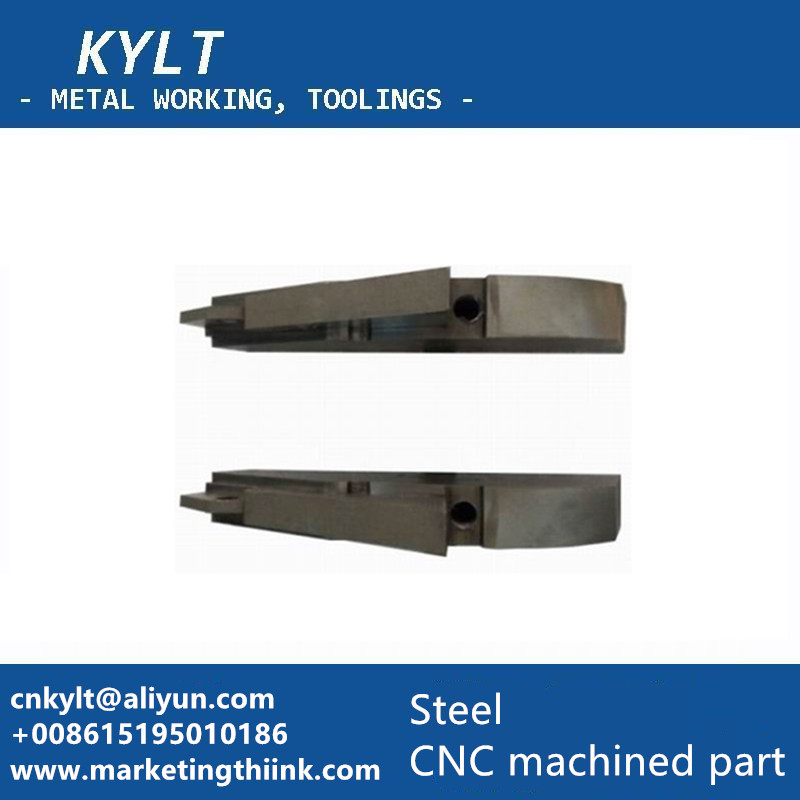
4) Choose the taper diameter of the reasonable precision grade when the thread diameter exceeds the general one; Choose the appropriate cutting fluid and reduce the cutting speed properly; Correct the coaxiality of the taper and the bottom hole of the thread when tapping the thread, adopt the floating chuck; Reduce the front angle and the rear angle of the cutting taper properly; Clean the burr produced by the grinding taper of the edge, and increase the cutting taper length appropriately.
5) Choose the appropriate taper diameter with small thread diameter; properly increase the front angle and cutting taper angle of the taper; replace the worn taper; select the cutting fluid with good lubricity.
6) Excessive surface roughness of threads properly enlarges the front angle of the tap and reduces the cutting cone angle; heat treatment is carried out to properly increase the hardness of the workpiece to ensure that the front face of the tap has a lower surface roughness value and select a lubricating cutting fluid; cutting speed is properly reduced; and worn taps are replaced.
KYLT Precision CNC machining services (milling & turning service), Fast prototyping, Fixture/Jig/Tooling making, Aluminum die casting & plastic injection parts. Email:cnkylt@aliyun.com +008615195010186
KYLT CNC Machining Services:
Home>CNC Machining Services>CNC Milling Services
Home>CNC Machining Services>CNC Turning Services
Home>CNC Machining Services>Rapid Prototyping Services
Home>CNC Machining Services>Injection Molding Services
KYLT CNC Precision Machined Parts:
Home>Precision CNC Machined Parts
Home>Precision CNC Machined Parts>CNC Precise Turned Parts
Home>Precision CNC Machined Parts>CNC Precise Milled Parts
Home>Precision CNC Machined Parts>Aluminum Machining
Home>Precision CNC Machined Parts>Magnesium Machining
Home>Precision CNC Machined Parts>Copper & Brass Machining
Home>Precision CNC Machined Parts>Steel Machining
Home>Precision CNC Machined Parts>Stainless Steel Machining
Home>Precision CNC Machined Parts>Plastic Machining
More information about Machining Technology: